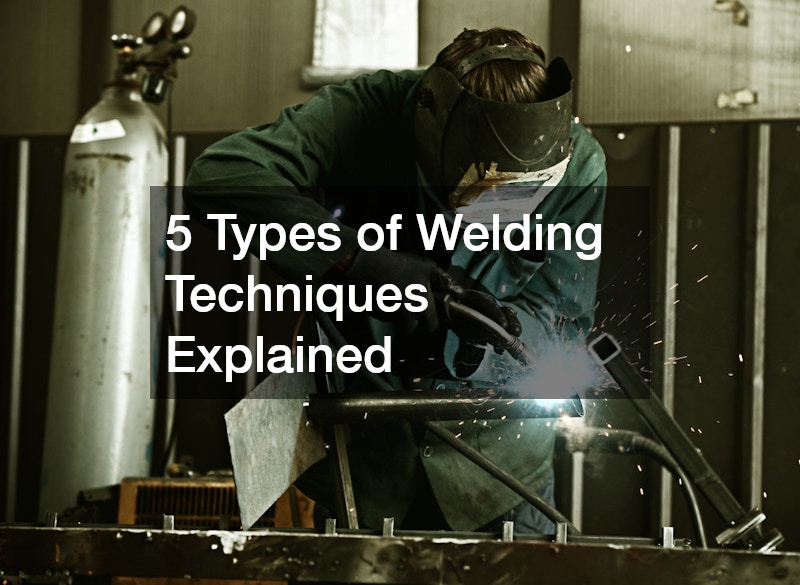
Welding plays a pivotal role in modern construction, manufacturing, and metalwork industries across Australia and the globe. It is the process of joining two or more pieces of metal or thermoplastics through heat, pressure, or both.
The result is a permanent bond that supports heavy loads, endures harsh environments and performs consistently in demanding conditions. Given its critical importance, understanding the various welding techniques is essential for tradespeople, engineers, and fabricators alike. Each technique comes with its unique strengths, applications, and considerations. This article explains five common welding methods and highlights how they differ, ensuring you can make informed decisions for your next project.
Shielded Metal Arc Welding (SMAW)
Shielded Metal Arc Welding, often referred to as stick welding, is one of the oldest and most widely used techniques in the welding industry. It involves the use of a consumable electrode coated in flux to lay the weld. An electric current forms an arc between the electrode and the metals being joined, generating enough heat to melt the workpieces and the electrode, which fuses the materials. As the electrode melts, the flux coating produces a gas shield that protects the weld from atmospheric contamination. This technique is prized for its simplicity and versatility. It works well with thick materials and in outdoor or windy environments, making it a reliable choice for structural steel, shipbuilding, and repair jobs. While it is not ideal for thin metals or high-precision projects, its robustness and portability make it a staple in many welding toolkits.
Gas Metal Arc Welding (GMAW)
Gas Metal Arc Welding, commonly known as MIG (Metal Inert Gas) welding, uses a continuously fed wire electrode and a shielding gas to protect the weld area from atmospheric gases such as oxygen and nitrogen. The wire electrode acts both as a filler material and as a conductor for the electric arc. This technique is known for its speed, cleanliness, and ease of use, making it popular in the automotive, construction, and metal fabrication industries. Unlike stick welding, MIG welding requires a more controlled environment, typically indoors, to prevent interference from wind or contaminants. The process produces clean welds with minimal spatter, reducing post-weld clean-up time. It is especially suitable for welding thinner materials like aluminium, stainless steel, and sheet metal.
Gas Tungsten Arc Welding (GTAW)
Gas Tungsten Arc Welding, also known as TIG (Tungsten Inert Gas) welding, offers precision and control for projects demanding high-quality welds. This process uses a non-consumable tungsten electrode to produce the weld. A separate filler material is typically fed by hand, and a shielding gas, usually argon, protects the weld zone from oxidation. TIG welding is highly regarded for its ability to produce clean, aesthetically pleasing welds with great structural integrity. It is the preferred technique for critical welds on stainless steel, aluminium, magnesium, and exotic metals. Its applications range from aerospace and automotive to custom fabrication and fine art metalwork. Despite its advantages, TIG welding requires significant operator skill and patience. The slower pace and complexity mean it is less commonly used in high-volume production settings, but it remains indispensable for precision work where weld quality is paramount.
Flux-Cored Arc Welding (FCAW)
Flux-Cored Arc Welding is similar to MIG welding but uses a tubular wire filled with flux. This method can be self-shielded or require an external shielding gas, depending on the application. FCAW is highly efficient and delivers deep penetration, making it well-suited for thicker materials and heavy-duty tasks. It is frequently employed in shipbuilding, structural steel fabrication, and outdoor welding jobs where high deposition rates are necessary. One key benefit of FCAW is its ability to operate effectively in outdoor environments without sacrificing weld quality, especially in windy conditions.
Oxy-Fuel Welding (OFW)
Oxy-Fuel Welding, also known as oxy-acetylene welding, is a traditional technique that relies on a flame produced by burning a mixture of oxygen and acetylene gas. This flame is used to heat the metal pieces until they reach their melting point, at which point a filler rod may be added to create the joint. While this method has seen a decline in popularity due to advancements in electric arc welding technologies, it still holds relevance in specific contexts. OFW is commonly used for metal cutting, brazing, and soldering, as well as for maintenance and repair work in rural or remote areas where electricity may not be readily available. Its simplicity and portability make it an appealing choice for hobbyists and tradespeople working in the field.
Welding is far more than just joining metal—it is a refined craft that demands technical knowledge, skill, and the right tools for each job. Whether you are tackling a heavy-duty industrial task or crafting fine metal art, selecting the right technique can make all the difference in quality, safety, and efficiency.
Shielded Metal Arc Welding offers rugged flexibility for outdoor work, while Gas Metal Arc Welding delivers speed and cleanliness in indoor environments. Gas Tungsten Arc Welding shines in applications requiring precision and aesthetic appeal, whereas Flux-Cored Arc Welding brings productivity to high-volume jobs. Finally, Oxy-Fuel Welding retains its value in fieldwork and cutting tasks. Understanding these techniques and their ideal applications helps ensure successful project outcomes and upholds the high standards of the welding profession across Australia. With the right approach and knowledge, welding continues to build the framework of innovation, infrastructure, and artistry for generations to come.